distribution warehouse
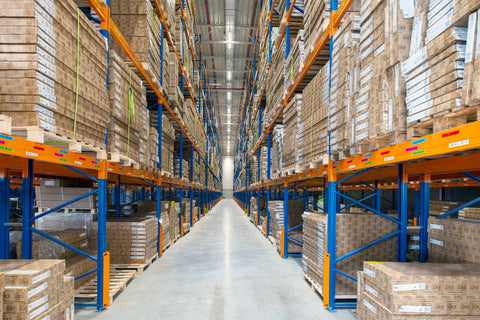
pallet racks in the distribution warehouse
A distribution warehouse is a central part of a company's supply chain and is used to store, process and distribute products to various destinations. It acts as an interface and only works within a logistics network. This primarily involves processing and fulfilling orders by receiving, temporarily storing and further distributing the goods. This organizes and handles the flow of materials between the manufacturer and the customer. They therefore play a crucial role in optimizing supply chains and ensuring efficient supply to customers.
Table of contents
Functions of a distribution warehouse
The main function of a distribution warehouse, distribution center, or logistics center is to transport products between manufacturers and customers. This includes various tasks such as receiving goods, storing them, picking them , packing them, and shipping them to end customers or retail locations. Therefore, they have a large product inventory so that the order, regardless of its size, can be processed quickly and delivered to the customer without delay.
advantages and challenges
The use of distribution warehouses offers a variety of benefits for companies in the logistics industry . These include:
- Improved efficiency: Distribution warehouses enable efficient management and sorting of goods. Centralized storage and distribution enables companies to optimize their supply chain flows and minimize bottlenecks.
- Cost savings: A centralized distribution center allows for the bundling of goods flows, resulting in significant cost savings. This includes lower shipping costs, reduced inventory and more efficient transportation routes.
- Faster delivery times: Companies can significantly reduce their delivery times. This is especially important in e-commerce and for companies that need to guarantee fast deliveries to customers.
- Inventory management: Distribution warehouses enable precise inventory management, resulting in a reduction in overstocking and shortages. The use of technologies such as barcode scanning and RFID contributes to the accuracy of inventory tracking.
- Quality control: Products can undergo quality control in the distribution warehouse to ensure that only flawless goods are shipped to customers.
challenges and solutions
Although distribution centers offer many benefits, they also come with challenges. Some of the most common challenges include:
- Customer requirements: Customers' increasing expectations for fast deliveries and transparent shipment tracking require constant adaptation of distribution processes.
- Cost management: Optimizing inventory costs while maintaining efficiency requires careful planning.
- Labor shortages: Recruiting and retaining qualified warehouse employees can be challenging.
- Technological integration: Seamless integration of warehouse management systems and automation technologies requires expertise.
- High initial investment: Building and setting up a distribution warehouse requires significant financial investment, including warehouse infrastructure, automation systems and technology.
Solutions to these challenges include investing in employee training, implementing advanced technologies, and working closely with suppliers and partners. The decision to use a distribution center depends on a variety of factors, such as business objectives, product range, and geographic reach. It is important to carefully weigh the pros and cons to find the best possible solution for a company's unique needs.
storage systems in the distribution center
In distribution centers, the focus is on fast and efficient operation, which is why various storage systems are used, including pallet racks and flow racks:
- Pallet racking: Pallet racking is widely used in distribution centers, ideal for locations with sufficient space and mechanical storage of pallets by forklifts , order pickers or pallet stackers . Direct access to the load units enables easy locating and loading/unloading, and the system is highly adaptable.
- FIFO flow racks: For space-saving, efficient storage in distribution centers, flow racks offer a dynamic solution in which palletized products are moved on inclined roller conveyors. The system based on the FIFO principle in particular ensures that the order in which the goods are removed corresponds to the order in which they are stored and is equipped with safety devices.
- Automated warehouse systems: Automated systems, including satellite carts and storage and retrieval machines, enable goods to be found, loaded and unloaded autonomously. From semi-automatic solutions such as the AR Shuttle to fully automated systems, they offer space and time optimization.
warehouse management systems
Warehouse management systems (WMS) play a crucial role in distribution centers. The software applications enable the control and monitoring of all warehouse processes. The functions of a WMS therefore include:
- Inventory tracking: Allows you to accurately track all products in the warehouse from their arrival to their delivery.
- Inventory management: Helps optimize inventory by reducing shortages and minimizing excess inventory.
- Picking: Supports the picking process by suggesting the most efficient ways to collect products.
- Packaging and shipping: Enables efficient handling of packaging and shipping processes, including the selection of the best shipping service providers.
- Reporting and Analytics: Provides insights into warehouse performance and efficiency through reporting and data analysis.
picking techniques for distribution warehouses
The picking technology for goods distribution centers, which enables the efficient reading, recording and input of information, is a basic requirement for the delivery of customer orders as desired and, above all, on time. Different picking methods have their own advantages and disadvantages. Choose the right solution for your distribution warehouse according to your requirements.
- Pick-by-Paper: Traditional method where the picker uses a printed picking list and checks off items manually.
- Pick-by-Tablet: A modern version that uses tablets to avoid manual rework in the system.
- Pick-by-Voice : Requires extensive Wi-Fi availability in the warehouse and a warehouse management system.
- Pick-by-Light / Put-to-Light: Uses light signals to guide the pickers.
- Pick-by-Scan / Pick-by-MDE (mobile data capture): Cost-effective solution based on barcodes.
- Pick-by-RFID (Radio-Frequency Identification): Uses RFID technology for efficient and error-free picking.
- Pick-by-Vision : Uses smart glasses or head-mounted displays (HMDs) for picking.
Future Innovations
The future of distribution warehouses will be shaped by technological advances and changing customer demands. Companies will invest more in technical developments to remain competitive and improve efficiency and accuracy. These innovations include:
- Automation: The use of robots and automated storage and picking systems increases the speed and precision of warehouse processes.
- IoT (Internet of Things): Connecting devices and sensors enables real-time monitoring of inventory levels and conditions.
- Artificial Intelligence (AI): AI algorithms optimize route planning, inventory management, and forecasting changes in demand.
- Data Analytics: Analyzing large amounts of data helps identify trends and patterns to make informed decisions.
In addition, the integration of sustainability practices into distribution processes will also become more important as companies strive to act more environmentally responsibly.