cross-docking
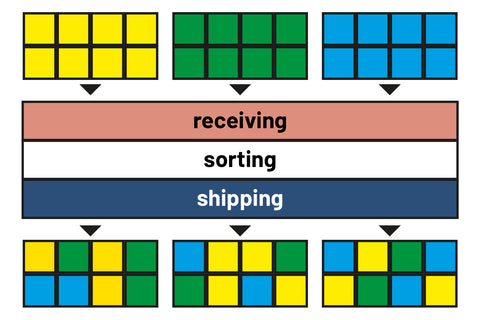
Cross Docking in Logistics
Cross docking (CD) is a type of goods handling. The aim is to no longer store goods, but to handle them directly and send them on. Cross docking can reduce storage costs and is particularly suitable for handling large quantities of goods.
Storage costs as cost drivers
Flexibility and cost pressure are fundamental issues when it comes to increasing a company's competitiveness and performance. Storage costs are a major cost factor for manufacturing companies. In particular, the costs of providing the necessary storage capacity and process handling are significant factors. Cross-docking logistics is one way to reduce storage costs and lead times.
Advantages of Cross Docking
The handling of goods without storage and inventory has advantages. Cross Docking
- reduces storage space requirements and inventory
- reduces the number of process steps and storage costs
- reduces throughput times
- improves timely deliveries
Typical variants
In practice, cross-docking logistics is used in three versions. It skips the steps of “storage”, “warehousing” and “removal”. The following distinction is made:
- Single-stage system (customer-oriented pre-picking): The sender or supplier notes the recipient's address on the goods. The goods are fully picked, packed and form a logistical unit. Forwarding to the addressee takes place unchanged and without any changes in the shipping area. Delivery takes place directly to the buyer via transshipment points.
- Two-stage system (upstream item-by-item picking): Also known as a "transshipment system", the supplier sends the goods unchanged to the transshipment point. There, they are re-picked into new units and delivered to different recipients. It is a special case of the multi-stage system and is also known as Break Bull Cross Docking (BBCD).
- Multi-stage system : In addition to the actual re-picking, further process steps take place here. The goods are not only re-sorted. Additional activities such as packaging or labeling also follow.
In retail, the distribution of full loads to branches is a typical variant.
Example of the process
A company sells products. These are manufactured both in-house and purchased. In the case of classic warehouse logistics, the company stores the products it has manufactured itself and also the other merchandise. Employees pick customer orders from the warehouse, pack them in the shipping area and shipping follows.
Cross docking is different: only goods from our own production are stored and picked. The supplier delivers commercial goods in time for the shipping date, and these are linked to the customer order in the shipping area.
Important prerequisites for successful cross docking
Smooth operations along the value chain are essential. Those involved in the supply chain must be transparently informed about the process steps; seamless communication from the manufacturer to the supplier to the customer is important.
As a result, meeting agreed delivery dates is crucial for success. The right products must arrive at the right customer in the right quantity at the right time. To achieve this, all supply chain participants must be integrated; the ideal solution is a real-time flow of data and information. Companies with the necessary IT solutions and complex storage technology have an advantage.
The aim of the inventory-free distribution method is to no longer store goods, but to immediately move them around and send them to the customer. The conception and integration of cross docking is a complex process that requires a lot of effort. The method is particularly interesting for companies that handle large quantities. It is used in retail, for example, where individual branches are usually supplied via central warehouses.